- Technology Sourcing Services
- DEX
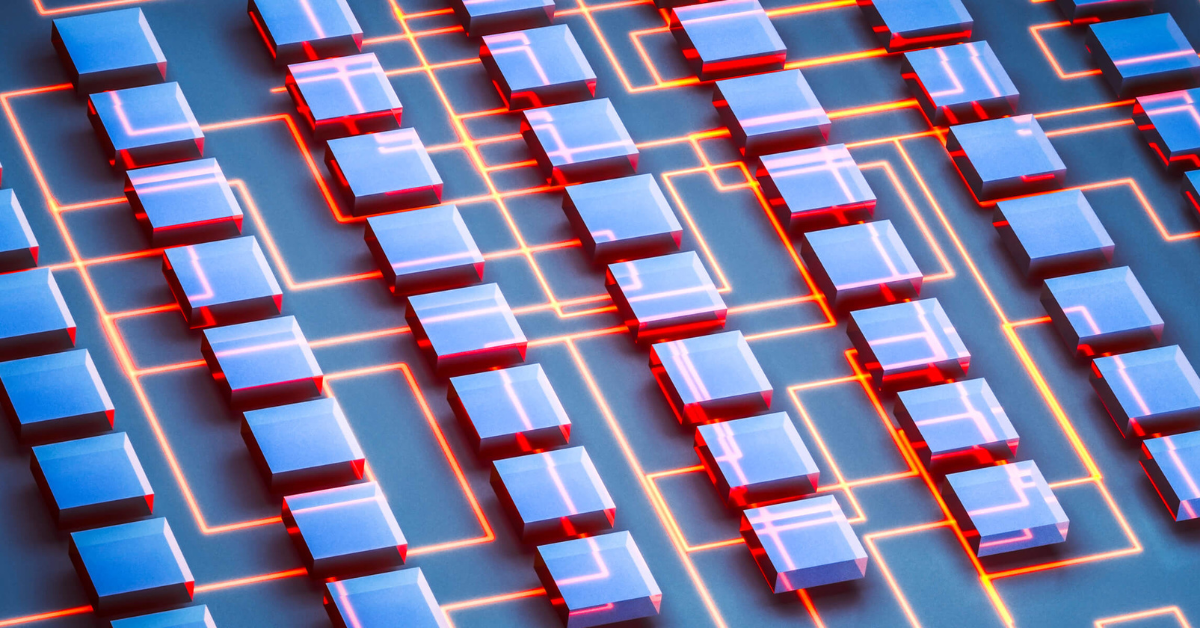
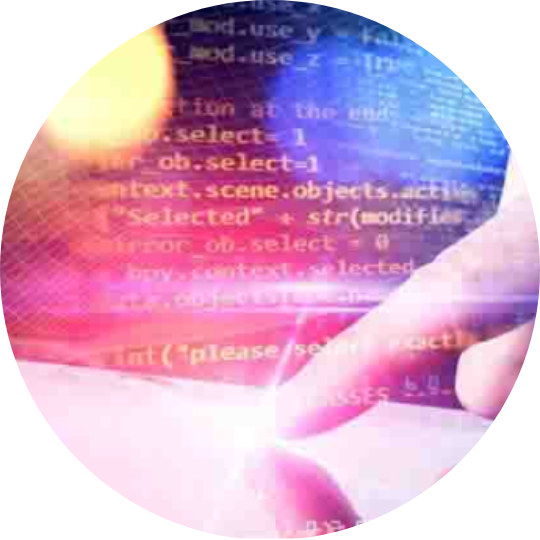
Marketing Compucom
“Where’s my Stuff?”
The “global supply chain” wasn’t always a household phrase. Then the pandemic hit.
Whether it is a scarcity of baby formula, widespread material shortages, or rising fuel and labor costs, supply chain problems are top of mind as they hurt consumers and employers alike this year.
Shipping delays, rising prices, and elevated demand are impacting virtually all industries, and employers are struggling to equip their people with the right technology for the job.
In a recent McKinsey survey, corporate CEOs said that supply chain disruptions are the greatest threat to company growth—more than the pandemic, labor shortages, and rising interest rates.
So how did we get here? When will it get better?
What Caused the Technology Supply Chain Crisis?
Computer chips were some of the first components to be disrupted by the pandemic. Coronavirus-related factory shutdowns blocked chipmakers’ ability to produce, leading to significant backorders and unpredictable lead times.
At the same time, the PC market was swamped when workers shifted to work from home.
Consumers wanted the latest phones, computers, and devices to effectively work from anywhere. Employers needed the right devices, tools, and hardware to support them.
Suppliers and major equipment manufacturers struggled to keep up with skyrocketing demand.
“While demand for semiconductors increased 17 percent from 2019 to 2021, there was no commensurate increase in supply,” according to the New York Times. “A vast majority of semiconductor plants are using about 90 percent of their capacity to manufacture chips, meaning they have little immediate ability to increase their output.”
“The need for chips is expected to increase, as technologies that use vast amounts of semiconductors, like 5G and electric vehicles, become more widespread.”
This January, chip delivery times (the gap between when a chip is ordered and when it is delivered) swelled to an average of 25.8 weeks, the longest wait time in five years.
The delay affects the production of everything from consumer electronics to cars, LED and lighting fixtures, and more. However, it’s not all bad news: the same report showed that for some suppliers, component lead times are “modestly” improving.
Technology Supply Slowly Adjusting to Demand
Like many, we hoped that workplace technology shortages would begin to improve in 2022 as enterprises adjusted to long-term remote work and the pandemic became more contained.
However, other events such as the war in Ukraine and more pandemic lockdowns in China have created other bottlenecks.
Gartner predicts supply chain constraints will continue for now, but 2022 will be a year of recovery during which “for the most part, supply will start to catch up to demand.”
While we may be in for a long haul as supply and demand balance out, their projections say that we could see a return to normal supply levels in Q3/Q4 2022 or early 2023.
Still, technology managers are facing day-to-day challenges and frustrated consumers asking, “Where’s my stuff?”
Three Ways to Support Your Organization
Practice Transparent Communication
Like consumer shopping, employees want clear information, an easy ordering process, and step-by-step updates on what’s happening. Whether delivery is two days away or two months out, people just want to know the status of their order! When lead times are constantly changing, communication is essential.
Organizations must manage those expectations internally, or turn to their technology partners to deliver transparent, step-by-step communication that never leaves customers in the dark.
Be open to alternatives
You’ve ordered 10,000 monitors. The exact ones you requested aren’t available for months, but similar alternatives are available in slightly different colors or models. If your priority is to get boxes in hands fast, you may want to consider a more flexible approach to ordering.
Expect your technology partner to understand your priorities and recommend alternatives when it makes sense. A reputable partner should find compliant alternative products when something is unavailable, and always keep you aware of what’s happening.
To minimize the effects of potential product shortages, we constantly track the availability of products and keep our customers aware of options and substitutes, creating a plan for a seamless supply of devices. At Compucom, order support specialists become experts in your organization’s preferences, products, and processes—so we can make strategic suggestions to help hit your goals.
Build Strategic Long-Term Relationships
Instead of a short-term fix (like paying a premium for one-off orders), now is the time to build technology strategies that can last throughout the supply chain crisis.
Technology partners and resellers can’t make products leave the factory any faster, but they can offer added value that improves the customer experience.
When assessing a vendor for your technology needs, consider whether they have certifications and authorizations from original equipment manufacturers (OEMs) and look for providers with deep existing relationships across the industry. Instead of just buying a product, consider whether a vendor can support and optimize the full lifecycle of your technology once you (finally) get it.
A Trusted Partner
We can’t fix the global supply chain—but we can make it easier for your organization to get what’s needed. Schedule a meeting with us to learn more.
RecenT
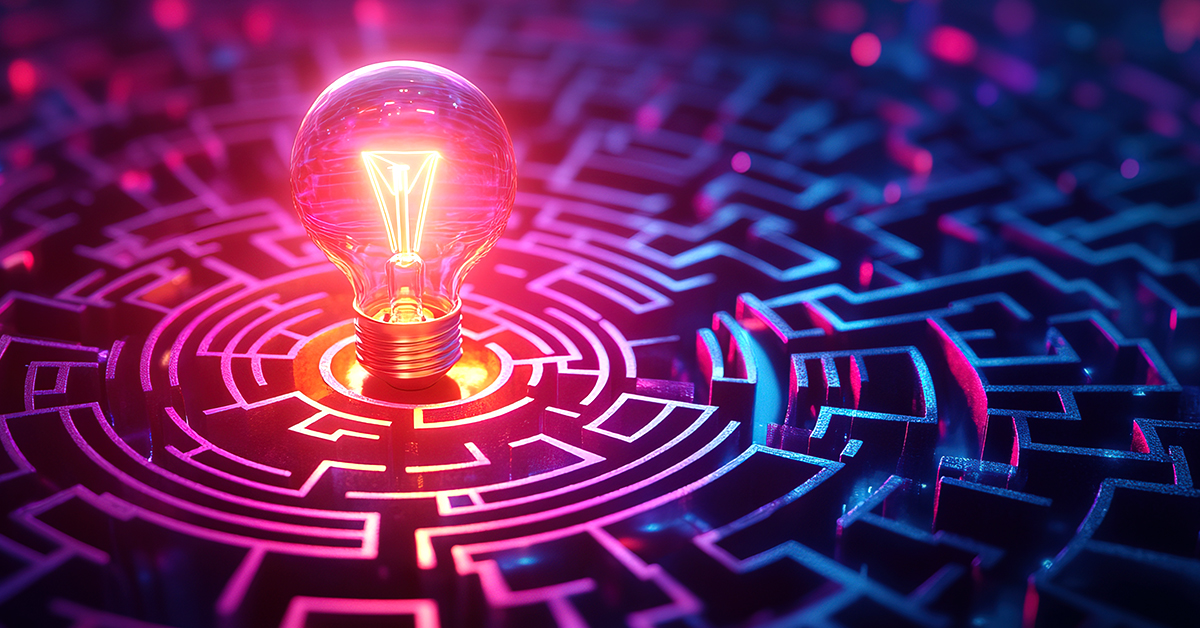
Future-Ready IT: Strategies to Optimize, Adapt, and Lead Through Uncertainty
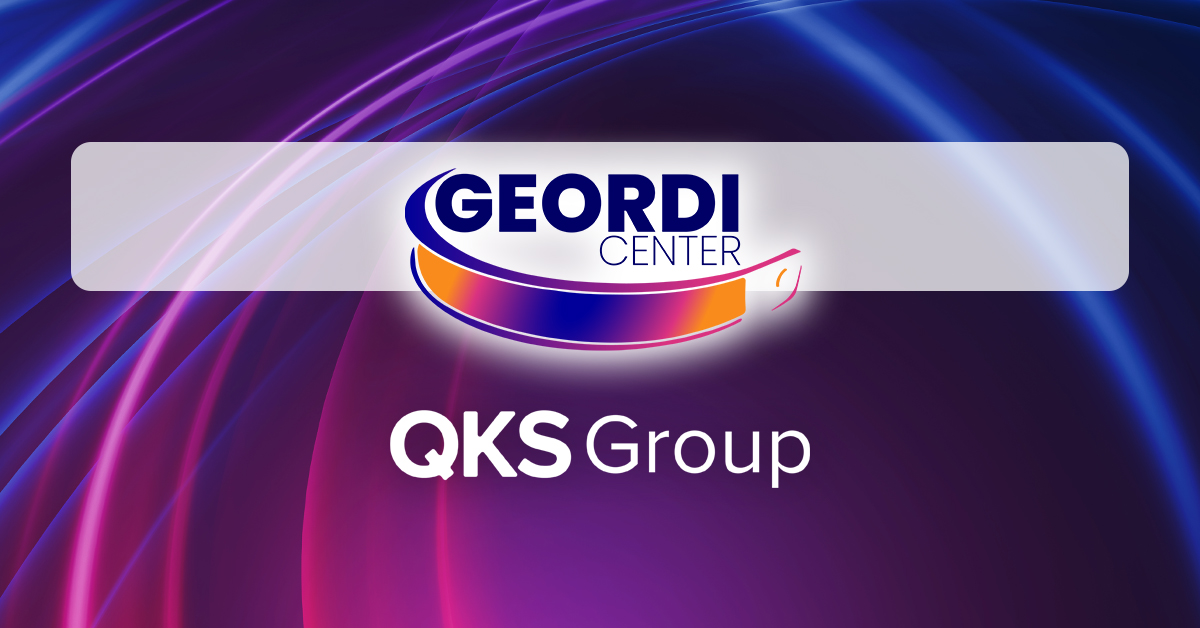
Reimagining IT with the FLO Framework: Inside Compucom’s Geordi Center for Interactive Managed Services and Digital Workplace Solutions
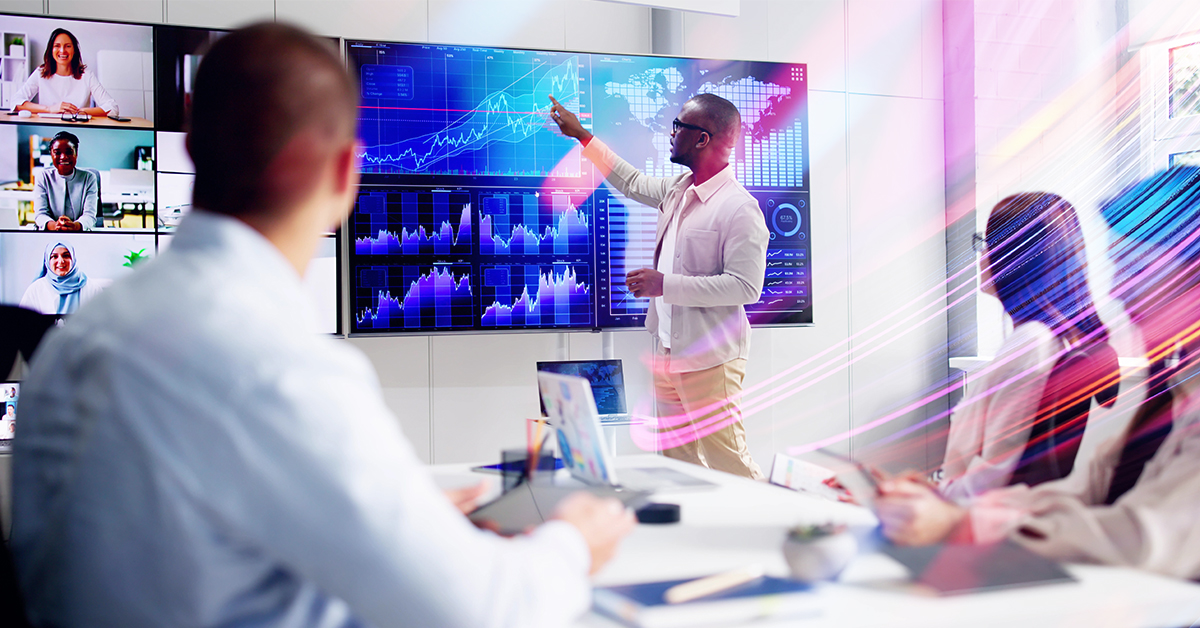
Opportunity in Uncertainty: Optimize Your Remote, Hybrid, or In-Office Setup
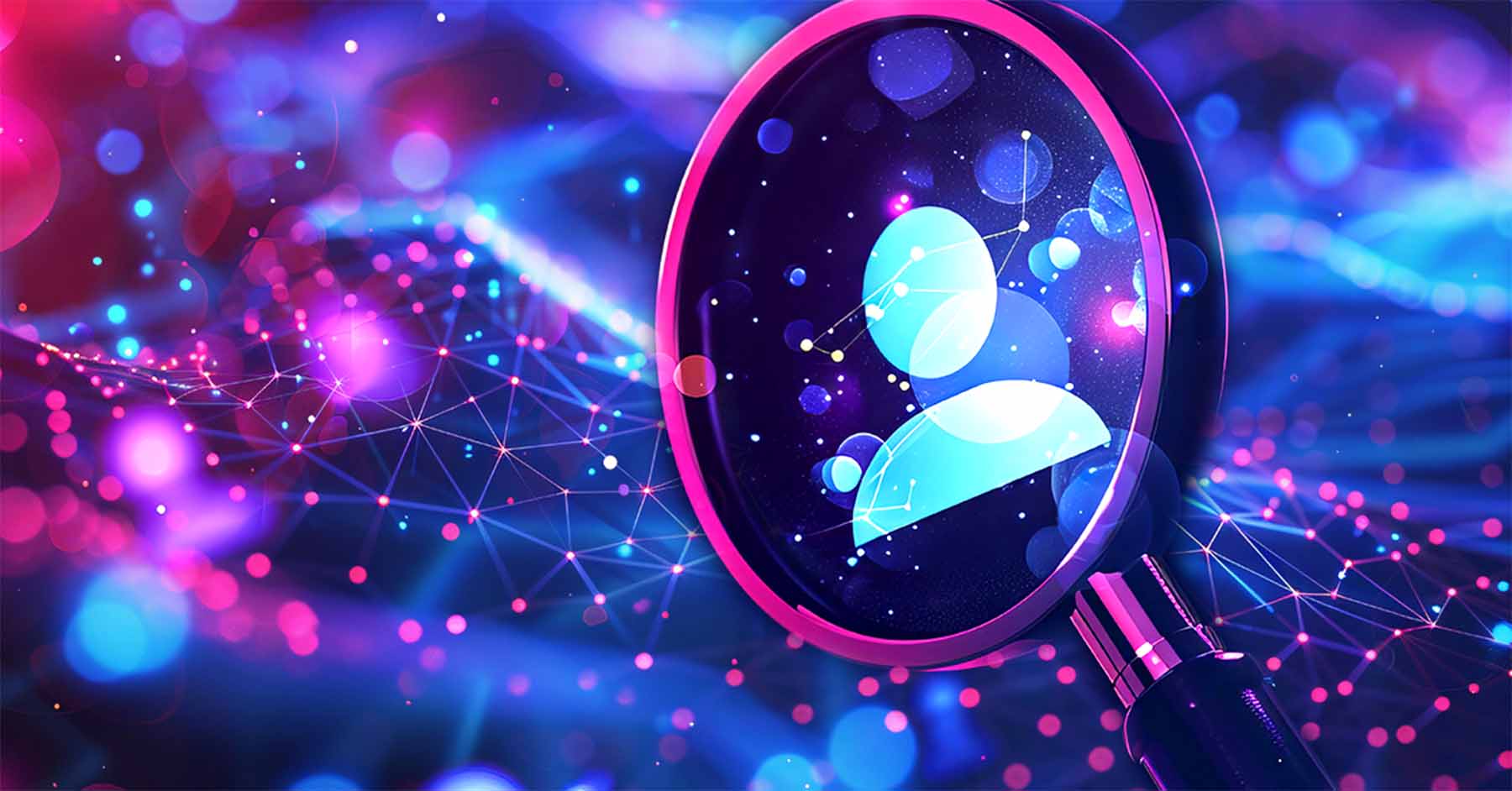
9 Ways Strategic IT Staffing Empowers Organizations
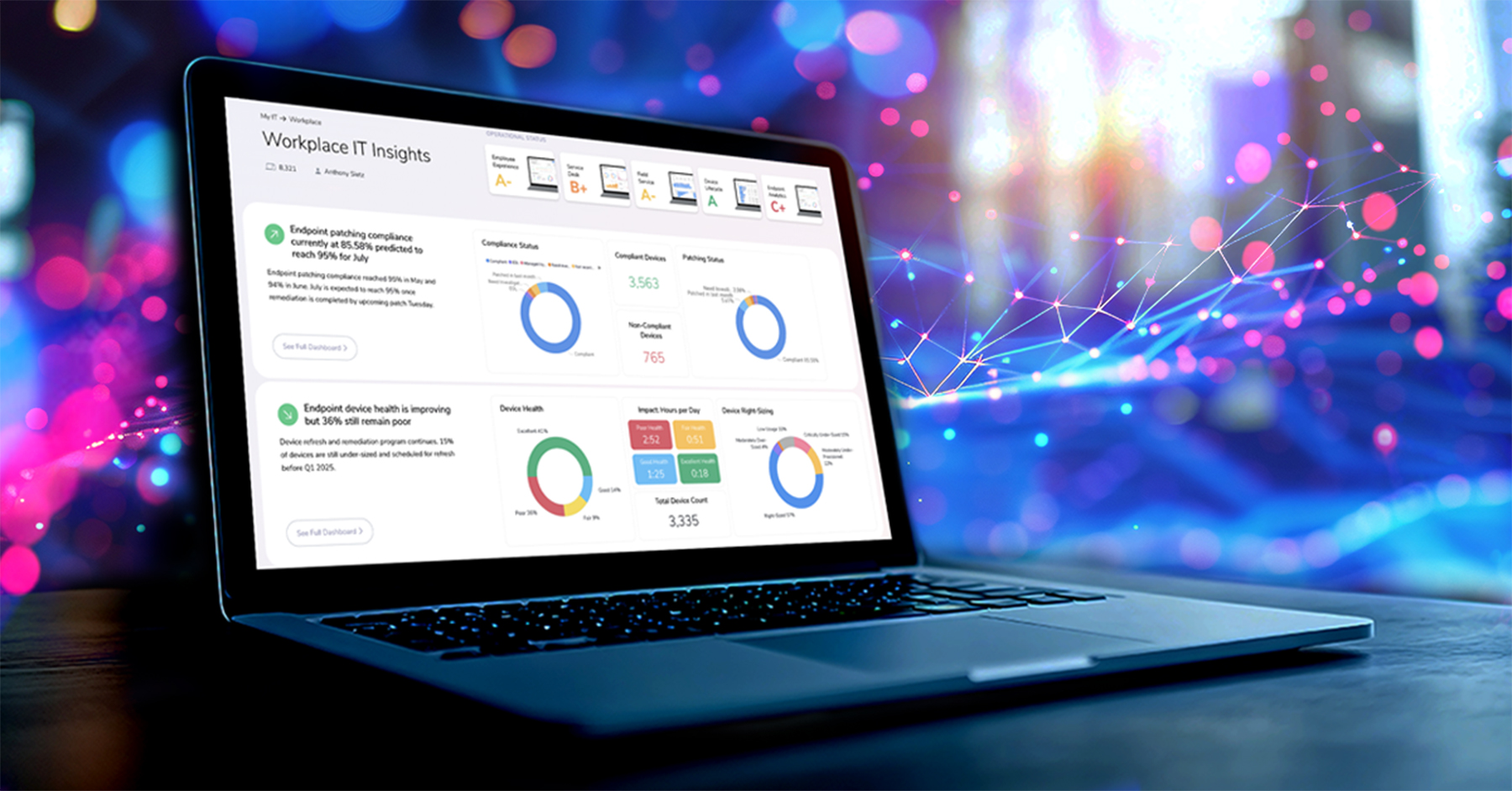
Case Studies: Asset Intelligence and Endpoint Compliance Made Easy
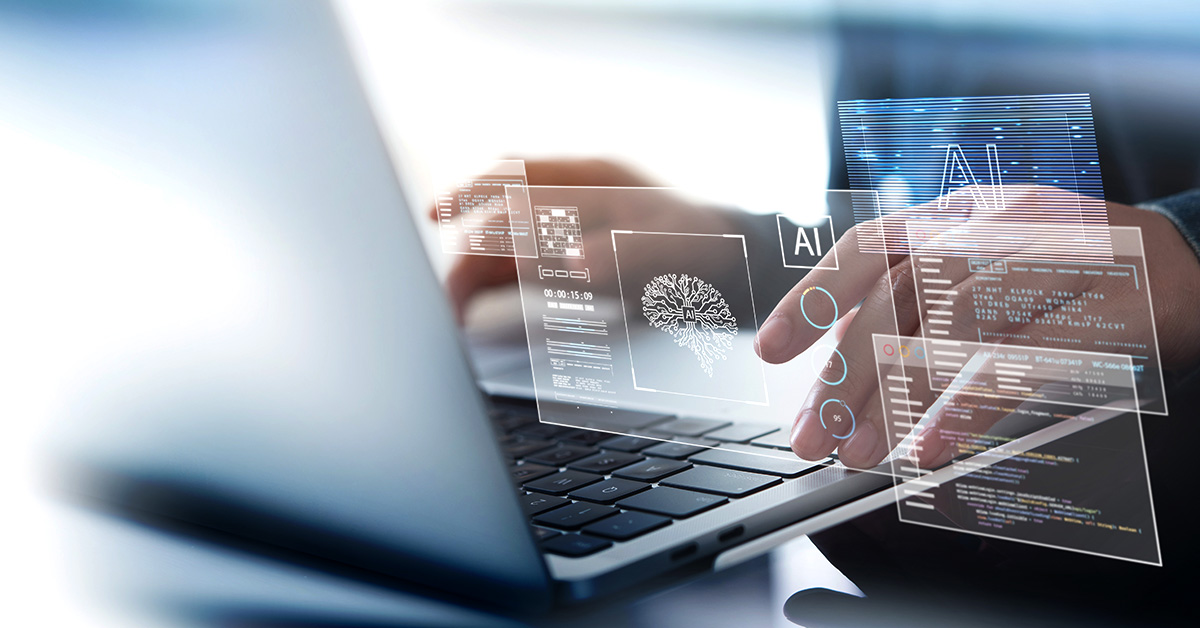
AI and the Enterprise: The Future of IT Management
TOPICS
Communication is Key in Ongoing Supply Chain Crisis
- Technology Sourcing Services
- DEX
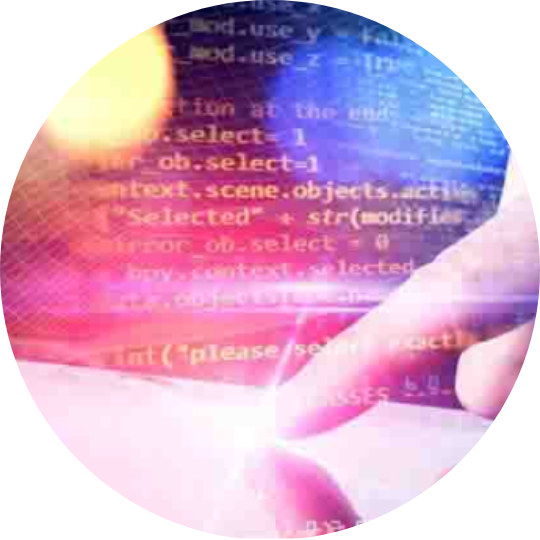
Marketing Compucom
“Where’s my Stuff?”
The “global supply chain” wasn’t always a household phrase. Then the pandemic hit.
Whether it is a scarcity of baby formula, widespread material shortages, or rising fuel and labor costs, supply chain problems are top of mind as they hurt consumers and employers alike this year.
Shipping delays, rising prices, and elevated demand are impacting virtually all industries, and employers are struggling to equip their people with the right technology for the job.
In a recent McKinsey survey, corporate CEOs said that supply chain disruptions are the greatest threat to company growth—more than the pandemic, labor shortages, and rising interest rates.
So how did we get here? When will it get better?
What Caused the Technology Supply Chain Crisis?
Computer chips were some of the first components to be disrupted by the pandemic. Coronavirus-related factory shutdowns blocked chipmakers’ ability to produce, leading to significant backorders and unpredictable lead times.
At the same time, the PC market was swamped when workers shifted to work from home.
Consumers wanted the latest phones, computers, and devices to effectively work from anywhere. Employers needed the right devices, tools, and hardware to support them.
Suppliers and major equipment manufacturers struggled to keep up with skyrocketing demand.
“While demand for semiconductors increased 17 percent from 2019 to 2021, there was no commensurate increase in supply,” according to the New York Times. “A vast majority of semiconductor plants are using about 90 percent of their capacity to manufacture chips, meaning they have little immediate ability to increase their output.”
“The need for chips is expected to increase, as technologies that use vast amounts of semiconductors, like 5G and electric vehicles, become more widespread.”
This January, chip delivery times (the gap between when a chip is ordered and when it is delivered) swelled to an average of 25.8 weeks, the longest wait time in five years.
The delay affects the production of everything from consumer electronics to cars, LED and lighting fixtures, and more. However, it’s not all bad news: the same report showed that for some suppliers, component lead times are “modestly” improving.
Technology Supply Slowly Adjusting to Demand
Like many, we hoped that workplace technology shortages would begin to improve in 2022 as enterprises adjusted to long-term remote work and the pandemic became more contained.
However, other events such as the war in Ukraine and more pandemic lockdowns in China have created other bottlenecks.
Gartner predicts supply chain constraints will continue for now, but 2022 will be a year of recovery during which “for the most part, supply will start to catch up to demand.”
While we may be in for a long haul as supply and demand balance out, their projections say that we could see a return to normal supply levels in Q3/Q4 2022 or early 2023.
Still, technology managers are facing day-to-day challenges and frustrated consumers asking, “Where’s my stuff?”
Three Ways to Support Your Organization
Practice Transparent Communication
Like consumer shopping, employees want clear information, an easy ordering process, and step-by-step updates on what’s happening. Whether delivery is two days away or two months out, people just want to know the status of their order! When lead times are constantly changing, communication is essential.
Organizations must manage those expectations internally, or turn to their technology partners to deliver transparent, step-by-step communication that never leaves customers in the dark.
Be open to alternatives
You’ve ordered 10,000 monitors. The exact ones you requested aren’t available for months, but similar alternatives are available in slightly different colors or models. If your priority is to get boxes in hands fast, you may want to consider a more flexible approach to ordering.
Expect your technology partner to understand your priorities and recommend alternatives when it makes sense. A reputable partner should find compliant alternative products when something is unavailable, and always keep you aware of what’s happening.
To minimize the effects of potential product shortages, we constantly track the availability of products and keep our customers aware of options and substitutes, creating a plan for a seamless supply of devices. At Compucom, order support specialists become experts in your organization’s preferences, products, and processes—so we can make strategic suggestions to help hit your goals.
Build Strategic Long-Term Relationships
Instead of a short-term fix (like paying a premium for one-off orders), now is the time to build technology strategies that can last throughout the supply chain crisis.
Technology partners and resellers can’t make products leave the factory any faster, but they can offer added value that improves the customer experience.
When assessing a vendor for your technology needs, consider whether they have certifications and authorizations from original equipment manufacturers (OEMs) and look for providers with deep existing relationships across the industry. Instead of just buying a product, consider whether a vendor can support and optimize the full lifecycle of your technology once you (finally) get it.
A Trusted Partner
We can’t fix the global supply chain—but we can make it easier for your organization to get what’s needed. Schedule a meeting with us to learn more.
Recent Blogs
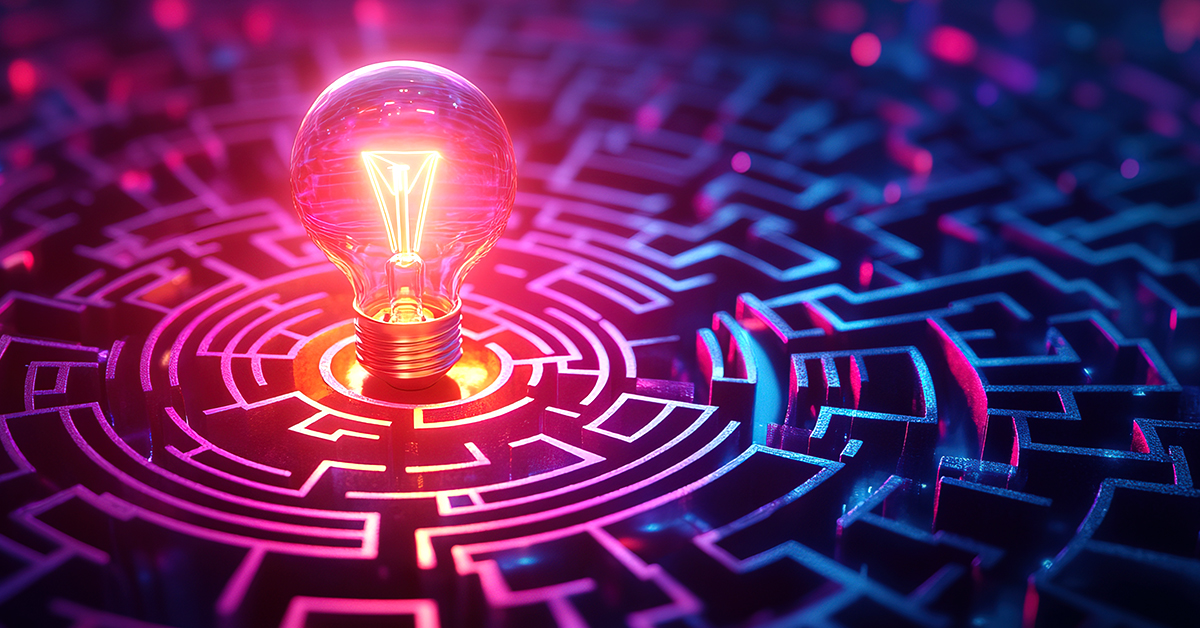
Future-Ready IT: Strategies to Optimize, Adapt, and Lead Through Uncertainty
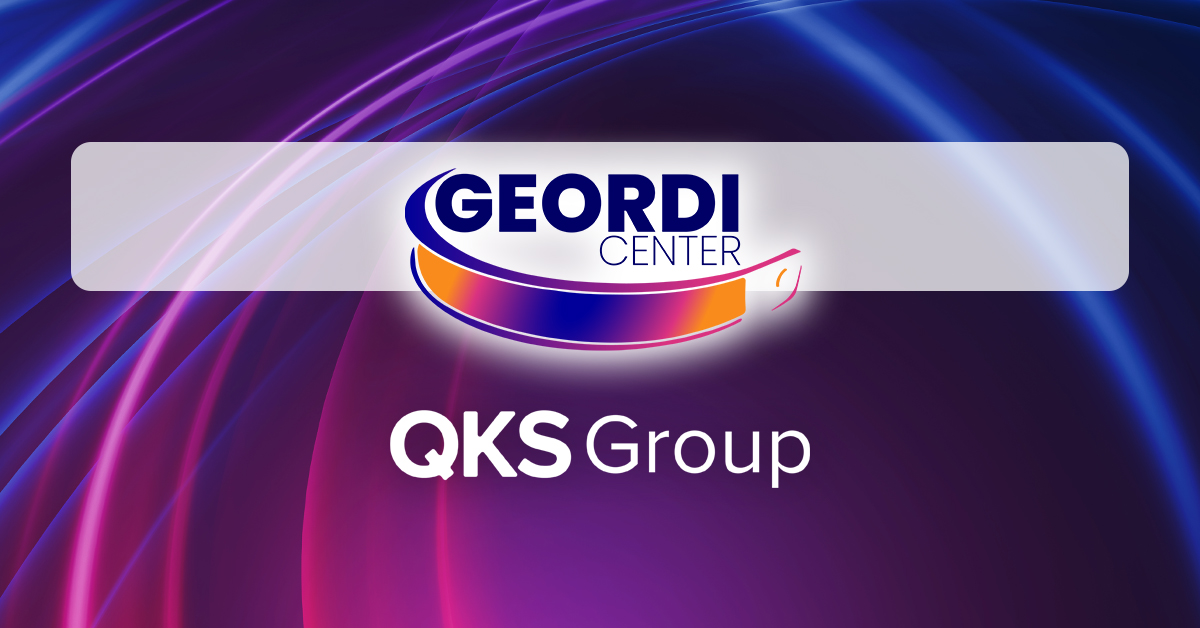
Reimagining IT with the FLO Framework: Inside Compucom’s Geordi Center for Interactive Managed Services and Digital Workplace Solutions
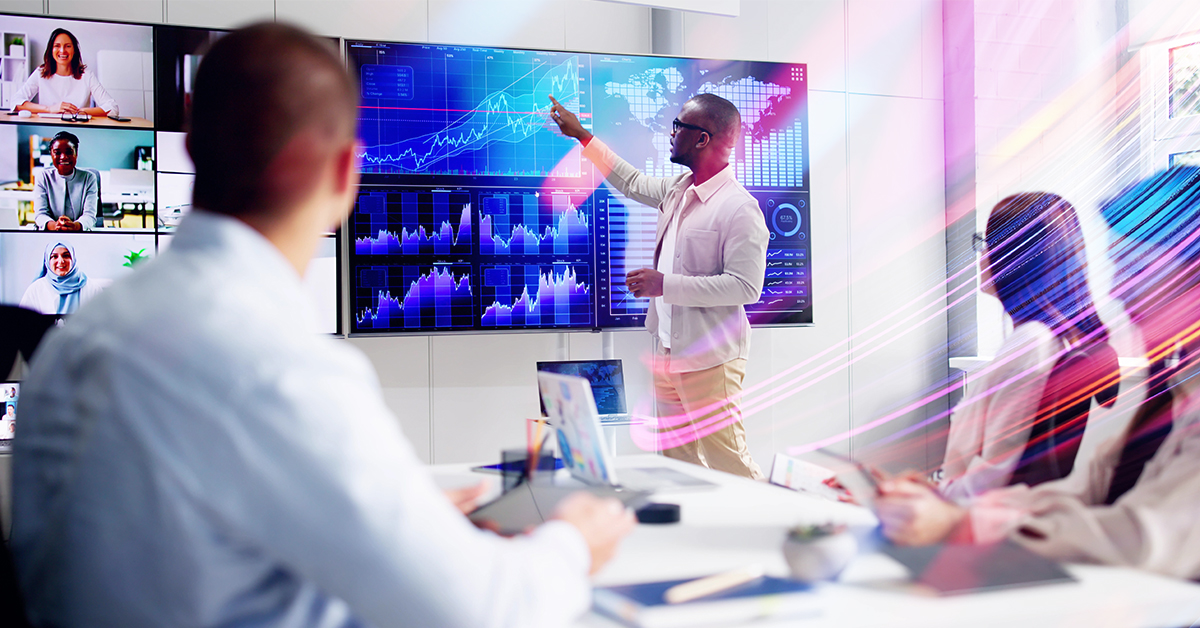
Opportunity in Uncertainty: Optimize Your Remote, Hybrid, or In-Office Setup
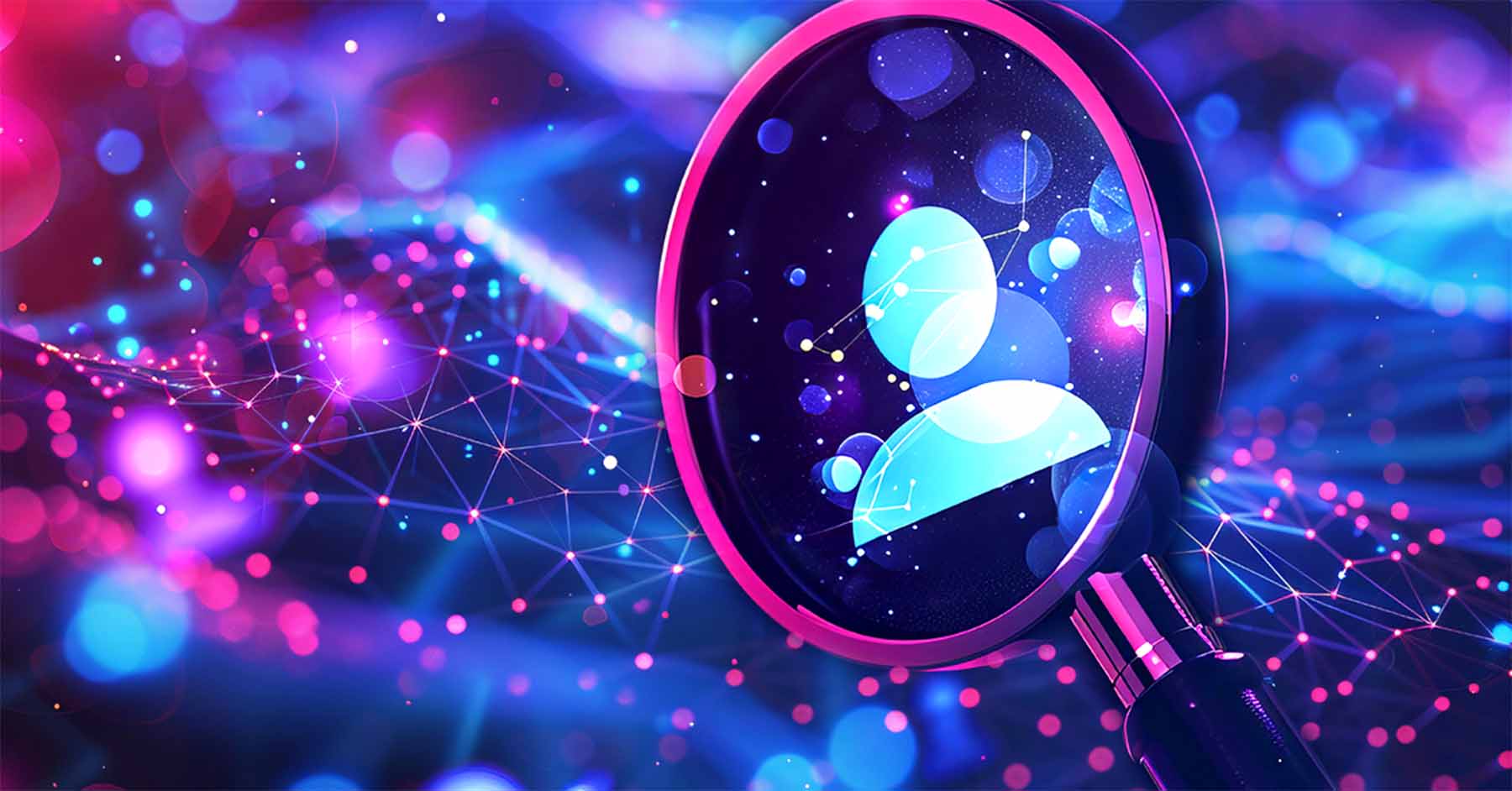
9 Ways Strategic IT Staffing Empowers Organizations
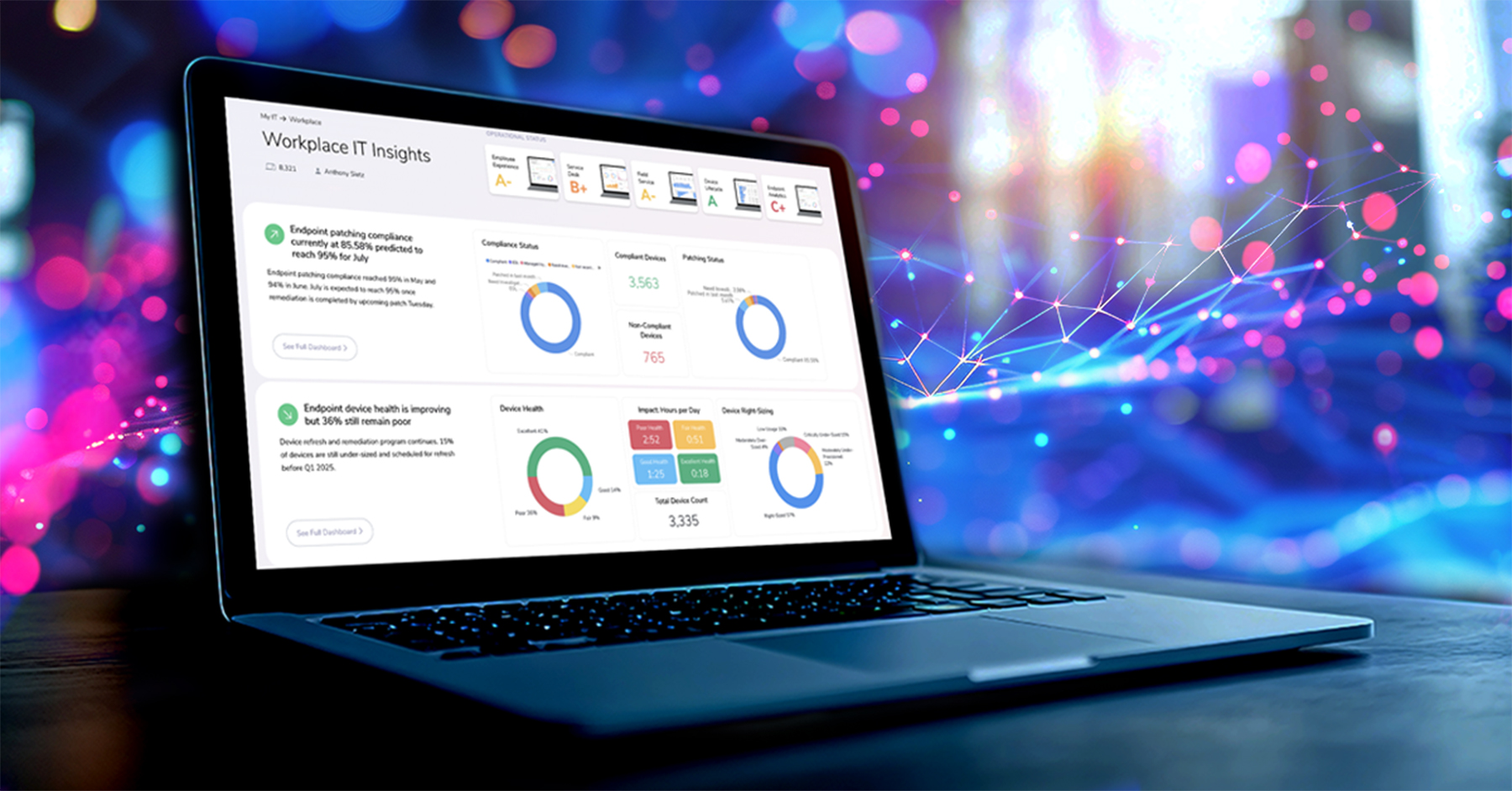
Case Studies: Asset Intelligence and Endpoint Compliance Made Easy
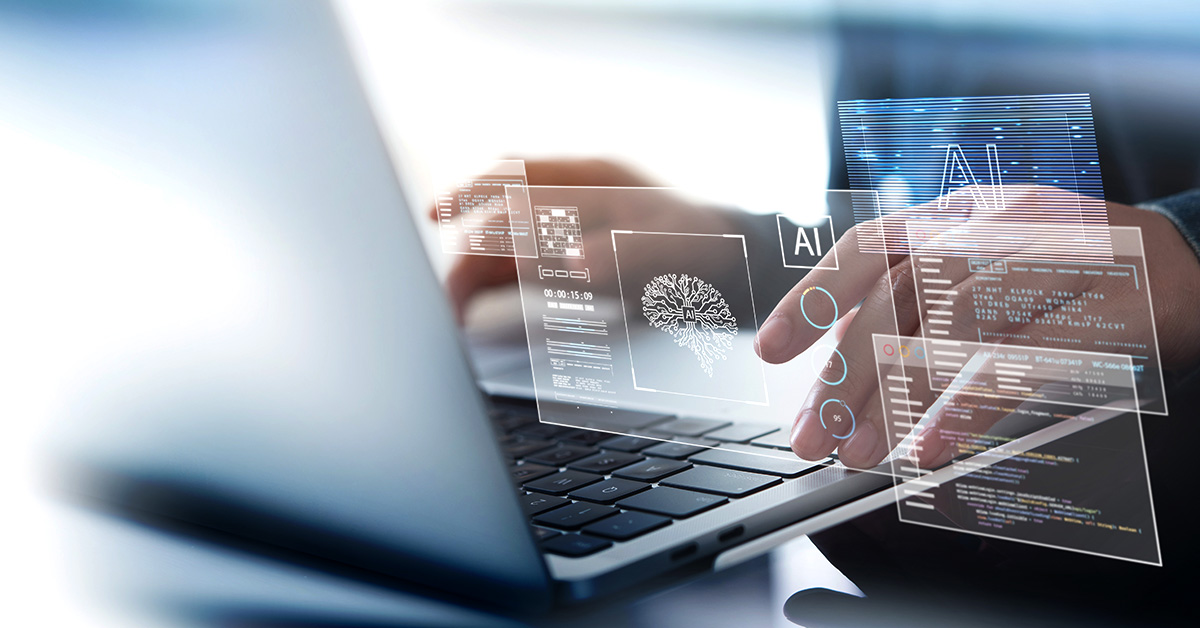